
According to pump manufacturers this loss of lubricity may be the difference between fuels from a controlled laboratory environment and a cost-conscious production environment.
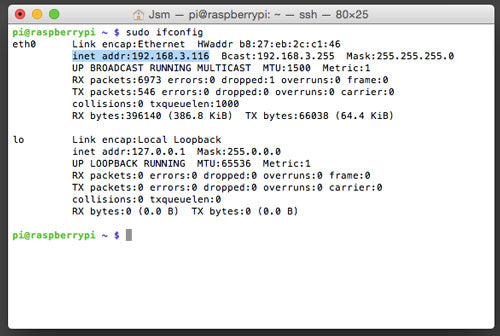
/how-to-change-ip-address-on-android-4588283-1-5c77295fc9e77c0001d19c87.png)
The topic of gasoline lubricity has recently become more urgent with the introduction of direct-injection gasoline engines, which will necessitate high-pressure gasoline injection pumps, a development that is most likely to place considerably more emphasis on the lubricating ability of gasoline, accelerating wear especially in rotary distributor fuel pumps. The history of fuel lubricity is associated with problems in engine performance as liquid-hydrocarbon based fuels must possess a minimum of lubricating ability to be able to protect high-pressure injection pumps and related fuel supply equipment from wear. For diesel fuel pumps and injectors, the liquid is the fuel itself and viscosity is not the key fuel property as one could profoundly expect. In hydrodynamic lubrication, a layer of liquid prevents contact between the opposing metal surfaces. The lubrication mechanism is a combination of hydrodynamic lubrication and boundary lubrication. Lubricity is the ability to reduce friction between solid surfaces in relative motion. To avoid excessive wear, the fuel must have some minimum level of lubricity. Some moving parts of diesel fuel pumps and injectors are protected from wear by the fuel.
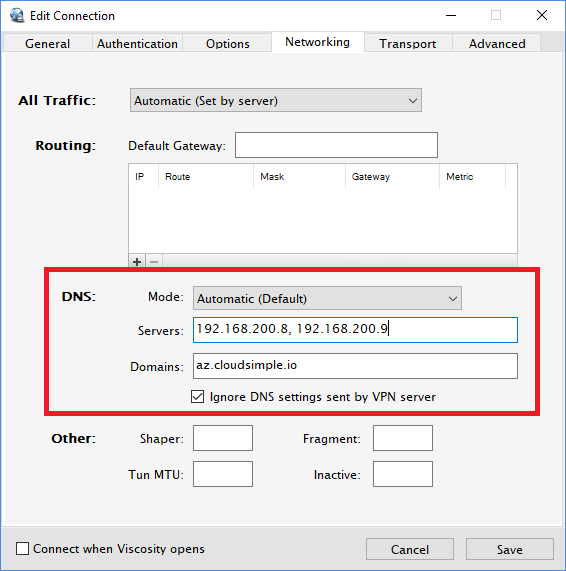
The lubricating ability of fuels, because of their very low viscosity, depends mostly on their boundary film-forming properties. It should be noted, however, that this definition was not strictly applied and many researchers carried out lubricity experiments on fuels based on their own understanding of the concept. Back in the 1960s, the term “lubricity” was defined by Appeldorn and Dukek as: “If two liquids have the same viscosity, and one gives lower friction, wear or scuffing, it is said to have better lubricity”.
